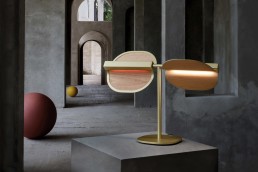
A New Leaf
Spanish lighting brand LZF‘s Omma collection was designed by Eli Gutierrez. She turns LZF’s well-known wooden aesthetic into a stylish family of lights inspired by trees and books.
Omma is one of the newest collections from Spanish lighting brand LZF. Inspired by leaves on tree branches and pages in books, the collection consists of two table lamps in single and two-leaf versions, a floor lamp, a wall light and four different pendant configurations.
Designed by Eli Gutierrez, the collection uses LZF’s patented Timberlite process, a very thin layer of wood veneer that creates the leaf shape that seamlessly attaches to the metal branch.
darc speaks with Sandro Tothill Caggiati, Co-Founder and Factory Director, about the inspirations and creative process of the Omma collection; its name derives from an old Frisian term meaning ‘breath’.
“Marivi Calvo, LZF’s other Co-Founder and Art Director, often looks to work with external designers because they each look at Timberlite with a different perspective. She is also constantly looking to work with female designers, as we believe they’re a really underrepresented group in general design. You have your stars, of course, but generally, it’s much harder to break through for women,” he explains.
“Eli came from a working background with Patricia Urquiola, whom she’d worked with for eight years, Philip Starck whom she worked with for a couple of years, and Iranian-French architect and designer India Mahdavi.
“Eli’s approach to designing with us was very cool. She took into consideration our work with wood and identified a concept. She linked that wood comes from trees, trees have leaves, and trees make paper for books, which also have page leaves. When you look at Omma, it looks like an open book. So, when you think of Omma, it’s a reflection and chain of thoughts that started with LZF’s relationship with wood.”
The collection’s design journey took longer than planned due to a change in the technical team at LZF during the process. “New people who came into the tech office inherited the work of previous people. And therefore, I think that in that sense, it was unfortunate because it meant that they inherited design, which had already begun and meant that any new ideas were not easy to put in. We had to finish what was started and finish it the way it was started because so much had already happened and so much development had taken place. It was literally picked up at 75% completion.
“The new tech office started at 75%, but rather than that meaning only 25% of the development time was left, the developing time was over 50%. That was because they had to understand why it was designed the way it was. They then had to work out how to finish the designs and fix the issues that were happening with the prototypes without re-designing the whole fixture,” he explains.
It also went through numerous prototype stages, which Caggiati describes as “hell”. “Each leaf, or pair of leaves, needed to be able to move individually from one another in order to change the direction of the light. A rotation mechanism allows you to alter the light direction to one flat beam, or various angles and ceiling projection.”
The team were eager to not wrap the wood veneer around any form or structure, yet it would act as an actual leaf. “To do that, we had to create a sort of ephemeral, light, metallic structure, which resembled Eli’s original concept. Once that happened, we had the open book form, which we needed to stick a light source down the middle of. The obvious choice was a recessed LED fixed into the lamp.
“When you look at the light from below, you can’t see the LED light source. The light comes down through the sheets instead. You get a great quality of light on your surface, but you can’t see exactly where it comes from. It creates a much more agreeable atmosphere. “There’s no diffuser, all you see is the natural wood and a light glowing out of it.”
In order to combat the swivel movements of the lamp heads, which ensured they remained in place but weren’t too difficult to manipulate to discourage users, the team came up with a gear-like mechanism. “If they were too stiff, the leaves wouldn’t move properly, and if they were too loose, they would just flop down again,” says Caggiati. “We developed a wheel with little grooves, like a cog, that a small ball point screw would click into when the shade was turned. The challenging part was figuring out the groove depth, and we underwent three different test types to achieve this. We then had to make sure the production team were fully briefed on how tight to make these components to meet the required tension.”
Timberlite is LZF’s patented process of treating wood that allows them to use it in such thin layers. Caggiati explains a little more about the process, however, cannot divulge the brand’s secrets: “Timberlite is about half a millimetre thick. We buy the raw veneer and then we use the Timberlite process to treat the veneer. It’s not a chemical process, so it’s very clean; there are no residues. Really, it’s more of a process tied to art and graphics rather than industrial. We don’t have to spray it or paint it and there are no solvents involved in its manufacturing. So, once it’s been treated, it’s very stable and you can store it for quite a long time. It also becomes very easy to then cut without cracking. This allows us to cut it on the digital plotter so we can work with many different shapes.
“We have two ways of working Timberlite. Basically, we have the organic way, which are just shades, which are created using the natural veneer making the shapes. And then the metal skeleton is only there to hold the light source in place.
“Then you have what we call hard shades, which are all the shades that have an acrylic or a metallic frame, which is what gives the shape to the lamp. With the Omma, we had this metallic frame, but it had to be very light, and it had to be bendable. When we were planning on how to glue the wood to it, we decided rather than bring the wood right up to the edge of the metal frame and have it nice flush with the metal, we decided to leave it, so the metal gives it a slight frame.
“Normally, we would’ve made sure the wood sheet came right to the edge, but then you lose the beauty of that metal, which is an aesthetic quality. So, you get the effect of a metal frame, whether you’re looking at it from the top side or from the bottom side. It was a new way of glueing or putting wood onto a structure for us in this sense.”
The collection comes in four main metal finishes for the lamp frames: gold, nickel, matte black and ivory white and is suitable for many various environments from hospitality venues to residential spaces, as Caggiati describes: “I think when you have a family like Omma, it makes it open to everything. The wall sconce is below 10 centimetres, which is a rule in the United States in the disabilities act, which states a wall lamp cannot protrude from the wall more than 10 centimetres in a public building. You’ve got the table and floor versions, which are good for the home. You’ve got the ceiling versions, which are good for restaurants, bars, and cafes. And then you’ve also got the Omma line pendant, which is good for offices. As far as decorating your office with a decorative lighting fixture, it works well as there’s enough light on your table from the lamp.”
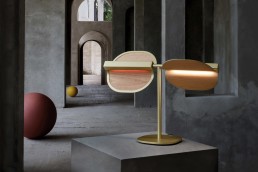