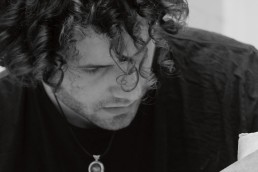
Federico Fiermonte
The brand new, brutalist-style, sculptural light Spira was presented at 2023’s Material Matters exhibition as part of London Design Festival.
Spira’s creator, Italian Federico Fiermonte is based in Helsinki, Finland and has only been designing and creating objects, experimenting with materials, and developing skills since 2021.
It is a spiral-shaped lamp, described by Fiermonte as “elegant, dynamic and delicate”. “It plays on the contrasts between a light and dynamic shape derived from nature, with an artificial, heavy, and robust material such as concrete, all with an added decorative touch given by the internal light that runs along the slender shape”, he adds.
The spiral shape is a common thread that runs through a lot of Fiermonte’s designs, something he explains as an “unintentional” consideration in his work.
“I envision this product primarily as a collector’s item, given its deeply artisanal creative process, which ensures that each piece is distinctly unique. When placed within a space, the Spira lamp is carefully designed to blend into its surroundings, asserting its presence with elegance.
“It effectively embodies the robust nature of the material that constitutes its essence, evoking a “brutalist” aesthetic. At the same time, as a decorative object, it generates a surprising contrast when placed in a minimalist environment, lending an unexpected element while curiously maintaining a sense of harmony within the environment.
“Exploring the interplay between light and concrete, I wanted to analyse my profound fascination for the field of architecture,” he continues.
“Concrete has made it possible to realise remarkable structures throughout architectural history, ranging from the iconic Pantheon dome in Rome where I come from, to complex constructions such as the Ganter bridge in the Swiss Alps. Within the context of architecture, I have always been captivated by the potential inherent in concrete. Spira draws great inspiration from the elegant spiral staircases of high-end buildings across the world with particular care of those part of the modernist style.
“For me, the key to achieving a harmonious and cohesive environment depends on the intrinsic relationship between design aesthetics and architectural materials.
“A line that guided me in the creation of this product – and which I think is always a characteristic feature of my way of conceiving objects – is to respect precise mathematical and geometric parameters, which vary from project to project.
“Working with light fascinates me enormously through the attempt of sculpting and giving shape to something so intangible and eternal.”
The concrete used by Fiermonte is composed of recycled aggregates to aim for a more sustainable product. The concrete is cast in a 3D printed mould made up of five parts, which proved challenging to create due its complex shape. “The most significant difficulty in making this piece was the creation of a mould that could lead to a clean and optimal result and produce precise edges. Making the mould is in fact 70% of the physical production work and it’s constantly being developed as I add improvements while continuing to work on the product,” he explains.
“In the initial stages, I experimented with compact foam moulds milled with CNC technique, subsequently I experimented with a silicone mould supported by plaster, and finally reaching the best result with a 3D printed mould with PLA made up of five parts.
“The particularly simple shape is complicated to obtain by casting the concrete, especially to remove once it has solidified.
“Within the lamp’s structure lies an armature crafted from hand-bent and welded rods, sourced from reclaimed metal waste, as well as aggregates repurposed from debris of different sizes (one to four millimetres) collected in the Otaniemi area in Espoo near Helsinki within the construction industry.
“For the functioning elements of the lamp I have been using a 12V DC transformer and a thin LED COB strip light. The implementation of a COB-type LED light strip allows the individual LEDs to be very close to each creating a seamless line of light that integrates perfectly within the design based on curves and lines.”
He continues: “Crafting an interior piece in concrete, using a recipe divergent from those employed in construction or infrastructure, offers a notable advantage. In this context, there is no imperative to meet specific standards of strength or durability like most structures that are concrete made. This liberates the creative process, fostering a greater degree of flexibility and experimentation, allowing for more focus on other artistic and design aspects.
“The choice to use concrete was partly driven by my desire to challenge public perception surrounding a material that I find captivating from an aesthetic standpoint, both in an attempt to highlight the beauty that can be obtained through this material and by taking it to its extremes.
“At the same time, I aimed to contribute to a more sustainable production approach by selecting components and conscientiously repurposing other waste elements.”
Once Fiermonte had settled on the design for Spira, his primary goal was to not change or make any compromises on the shape. This greatly impacted the process of creating and developing the mould. But it was all worth it for the designer as he achieved what he set out to, and all within just over a year.
www.fiermonte.design
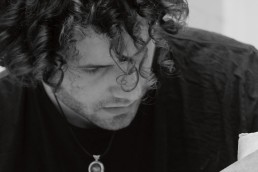