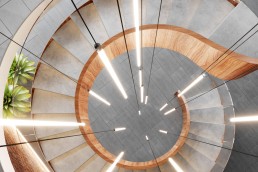
In Focus – Lysabel Lorenzo Truant intra lighting
Designer Lorenzo Traunt discusses his pendant light, Lysbel, for intra light.
What is the design concept behind Lysabel?
Lysabel was born as a straight line, hypothetically infinite, radiating its light 360°. The primal idea of Lysabel originated from the beautiful images of laser sabre battles in well-known science fiction movies. The whole project was illustrated through compelling images, reminiscent of the epic saga, with numerous characters wielding the lamp attached to the power cord. For example, the robotic multi-armed Grievous from Star Wars (who wielded four lasers) lent itself to being associated with the adjustable multi-armed Lysabel chandelier or the “en guard” position of one of the knights approaching the floor lamp.
The collection grew with the thought of light like a gash in the darkness, like a weapon to be wielded in a dark space to illuminate it, like a battle between opposing entities such as light and darkness.
How long have you been working on the collection?
The Lysabel collection was born in 2019 and developed over a few months with increasingly elaborate concept sketches and an initial 3D-engineered design equipped with all the essential components. In 2020, it was sent to Intra lighting, with the first prototypes unveiled in 2022.
What was the most challenging aspect of this project?
Managing the uniformity of light along the light rod. In my initial drawings, I identified both a 360° spread and a predominance of light on one side, without compensating for the opposite side. The hypothesis could only be checked in the prototyping phase, thanks to the photogoniometer provided by Intra. This device allowed us to assess optimal light diffusion with precise data, without bothering the view.
Another challenge involved designing the connection between the light rod and the power cord. The detail borrowed from the particulars of irons has been simplified and embellished. This detail personalises the lamp and makes it ready to become a horizontal, vertical or tilted element as desired.
What materials and design processes are used?
The basic materials are aluminium and acrylic glass (PMMA), both of which are 100% recyclable. The profile of the acrylic glass is obtained by an extrusion process that easily allows for varying lamp lengths and improves production by optimising it in terms of assembly time and production adjustment. High-quality LED strips can be cut to size, allowing for high production flexibility. The light sources have high-quality parwww.intra-lighting.comameters: Hi flux LED strip, CRI>90, MacAdam<2, and with a wide range of colour temperatures: 2700K, 3000K, 3500K, 4000K. The design process begins with imaginative assumptions. These ideas converge into thoughtful formal choices that undergo verification in the engineering and prototyping phase. Subsequently, they are further examined in the photometric results, utilising tools such as the photogoniometer. This meticulous approach aims to achieve optimal functionality and manageability.
What technologies are used?
The frosted opalescent acrylic glass tubes are extruded by calculating the exact coverage of the opalescent compound so that the light is diffused evenly without the bright dots of the LEDs being visible, but without the diffuser finish being able to cover too much of the light emission. The aluminum body, including the ball joint and all visible metal details, is offered with a choice of finishes: gold, onyx, and bronze in coated or brushed variants. The components are of high quality, and the ballast operates at 24V, maintaining a constant voltage. The light source consists of long flexible webbing that can be cut at will, carrying on board numerous LEDs juxtaposed one to the other and electrically connected.
Despite its slender appearance suggesting fragility, the collection is surprisingly resilient and manageable.
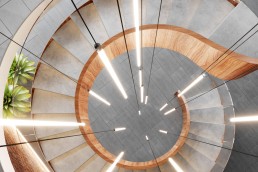