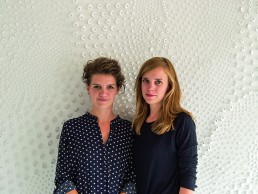
Alissa van Asseldonk & Nienke Bongers
Founded by Alissa van Asseldonk and Nienke Bongers, Alissa + Nienke is a material research and design studio with a unique interpretation of surface design. Here, in her own words Alissa van Asseldonk talks materials, innovation and design.
The basis of our studio is a joint urge to experiment, we met at Design Academy Eindhoven when we were both doing our internships, and we really felt the need to create for ourselves. That is when we started a ‘material get-together’ resulting in our successful product line Pigments & Porcelain. The experimentalism and research was always there, but it wasn’t until a few years later that we deliberately transformed our studio into a much wider approach to materials and applications focussing on the manipulation of flat materials to make them pop-up, move or elevate and to apply them to our daily living environment – this is strongly influenced by our aim to trigger curiosity and interaction.
You could say that the experiments we do in our studio often surprise or trigger us to such an extent that we really want to translate them into bigger, durable and applicable materials or products that can be experienced by a broader public. For us, material research is really about bringing this experience to people. This means researching human perception, creating new materials to improve daily life and exploring what our future environments will look like. Over the last few years we developed our own human-centric approach to material research and design, specialising in surface design.
Our team consists of the two of us, often supported by freelancers, trainees or interns. As Nienke and I are quite different, we know where both of our strengths lie and aim to empower those by dividing tasks. This happens in a practical sense, but also within projects. Where I am the structured and analytical one, Nienke has the free, crazy mind. So my strengths lie in the research part looking into material properties and functioning, Nienke’s strength is the crazy patterns and detailing. My focus is more graphical and leans towards colour use and combinations, Nienke leans towards tactility and touch. It’s a constant synergy in diverging and converging a design from our own angle, to later bring it together in a brainstorm like meeting. This can sometimes result in intense discussions but always generates a stronger end result.
We often collaborate with specialised companies to push the technical boundaries of our designs, this keeps us fresh, we feel like we’re constantly learning new things. The challenge is to apply this knowledge to your own design perspective, which is also really fun.
Material means so much to our brand: tactility, movement, softness, stimulation, discovery, and optical illusions. We really do believe that in a world that’s getting more digital it’s important to think about our daily surroundings, our work and living environment. Our studio’s aim is to adjust the environment we spend most of our time in, in order to enrich our lives, and we do so by creating materials that speak to all the senses. We see materials as the bridge between your body and the space surrounding you.
We often use readily available materials and techniques but tweak and manipulate them to get something new. This process is often very interesting; when we actually make an end result that can be applied it can make people perceive a space or an activity differently. We want to think beyond the ordinary, could a wall be more than a wall? Our process is full of what ifs.
The first project in which we’re working with light is a good example of this, it’s called Woven Light and first began with us winning a Renault Design Award for a lifestyle product concept: layered window blinds that create new patterns due to cut outs and transparency. We didn’t develop this concept into a real product because it felt quite flat and we had a feeling that we could take it a step further, we let the project rest to pick it up again at a later date (this often works quite well for our company). We were already very interested in traditional weaving techniques and at the time we had an intern working with us who specialised in textiles who was working on ton-sur-tun weavings in black and white for the studio, we decided to work with a semi-transparent material, which enabled us to discover the inner structure.
Analysing what made the weavings interesting triggered us to work with porcelain, a material we were already familiar with and had access to. We had the material Keraflex lying around the studio so tried some tests in common weaving that we fired in our kiln. Keraflex is a kind of porcelain foil, a sheet material that isn’t known for its most innovative applications so it was a challenge to use it in a not so obvious way.
Our studio is part of a creative co-working hub in Eindhoven (which we set up ourselves) all kinds of facilities are available to us, which means we can do rapid prototyping in-house in metal, wood, ceramics, printing etc.
When the first tests came back from the kiln we decided to combine our research into transparent patterns for the Renault Design Award, a decision that was the basis of the development of Woven Light.
We started creating digital patterns that we later cut using paper as the initial material so we could physically weave it, later with a local laser cutting company we tested the Keraflex and after much experimentation discovered how to laser cut it in a detailed way.
As the material has a certain thickness, we had to create patterns that were actually weavable without the material breaking. Porcelain has very nice qualities and transparent characteristics, but also shrinks almost 20% when firing in a kiln. It was a big challenge to create a woven structure that wouldn’t pull or tear itself apart while firing and shrinking.
It became a quest, almost a puzzle, to create interesting patterns that changed with the light while not breaking it in the process. Therefore, and this happens in many of our projects, design choices are actually a direct result of the technical process. With every piece of knowledge we gain, ‘design rules’ within a project pop-up. Our projects are always creating their own framework, as if we’re battling with the material itself.
When we succeeded in creating the porcelain, woven sheets, we realised the material was very fragile and proceeded to try round shapes, which are generally stronger. Again, an adaptation had to be made in the weaving patterns to create round shapes. Because of the strength issue one of the ‘design rules’ became: in every weaving, horizontal, vertical and diagonal directions had to be combined. This resulted in a collection of possibilities that you can now see in our prototype collection.
We chose not to glaze the porcelain, this could have made it stronger as it adds another layer but we felt that the porcelain is so beautiful already, almost skin-like. Unglazed it also created more of a surprise effect.
We are always eager to discover and show all sides of a product or material, literally and metaphorically. We don’t just think about the flat front, what happens on the side? What happens when the material moves? What happens when you move? Every tiny detail interacts differently with light. For example, in our three-dimensional wall coverings, we actually print all sides, even the interior sides. We create very subtle gradients that can be enhanced by the interaction with light.
Every material has a different effect while interacting with light, for us it’s very interesting to think about the application: where is our product or material going to live, who is interacting with it and when? While testing and prototyping we work with different light sources to see how our materials react to it.
We are currently working on a new concept for LED lighting, though it’s all still very premature, we hope to give a sneak-peak during the next Salone del Mobile.
As well as that, we are in the process of testing and further developing to integrate lighting in the design of some of our existing projects, such as the Dangling Mirror.
The biggest challenge as a small studio with the aim to innovate is that prototyping can sometimes be very expensive. How do you afford a long process of research and development? Our way is to constantly improve and build on what we have. We’re not afraid to show ideas or concepts to the world. For us making others around you enthusiastic actually results in great partners to work with.
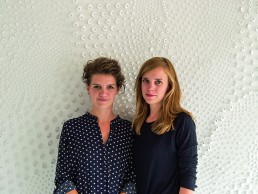